5 Use Cases for Real-Time Data in Business Automation
Explore how real-time data is revolutionizing business automation across supply chains, fraud prevention, inventory control, customer service, and maintenance.
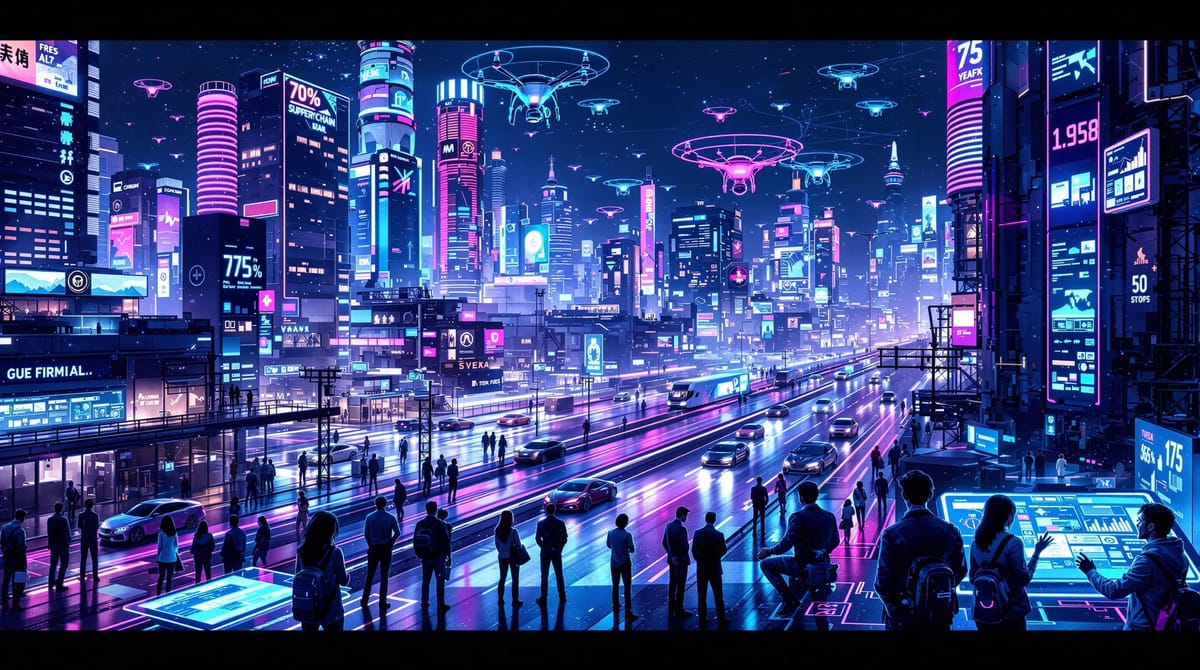
Real-time data is transforming business automation, making processes faster, more accurate, and cost-effective. Companies using real-time systems report faster decision-making (63% improvement), reduced errors (40%), and significant ROI (up to 300%). Here are the five key areas where this technology is making an impact:
- Supply Chain Management: Improves inventory turnover (15-30%), cuts order delays (20-40%), and reduces transportation costs (10-20%).
- Fraud Prevention Systems: Detects fraud with 95% accuracy, lowers false positives (<1%), and speeds up response times to under 100ms.
- Smart Inventory Control: Reduces stockouts (35-60%), saves on inventory costs (15-30%), and boosts restocking speed (50-70%).
- Customer Experience Automation: Increases conversion rates (15-20%), enhances order values (+30%), and delivers responses in under 500ms.
- Equipment Maintenance Systems: Cuts downtime (25-40%), reduces maintenance costs (15-30%), and predicts failures 30-90 days in advance.
Real Time Analytics Business Use Cases
1. Supply Chain Management
Real-time data is reshaping supply chains, driving measurable improvements:
Performance Indicator | Typical Improvement |
---|---|
Inventory Turnover | 15-30% increase |
Order Fulfillment Speed | 20-40% reduction |
Forecast Accuracy | 25-35% improvement |
Transportation Costs | 10-20% decrease |
Take Coca-Cola as an example. The company automated reporting for over 200 million data lines across 100+ systems using advanced BI tools. This shift saved 40+ hours of manual reporting each week and improved demand forecasting accuracy by 18%. Their system now automatically triggers replenishment orders based on real-time regional sales data.
AI-powered supply chains are also achieving faster results. According to McKinsey, they respond to market changes 52-68% faster. Google CEO Sundar Pichai emphasized this at the 2023 Google Cloud Next event:
"Real-time data integration will separate market leaders from followers within 18 months."
Key components driving these outcomes include:
- IoT sensors for continuous warehouse monitoring
- Cloud-based systems for coordinating across multiple locations
- Machine learning algorithms for predictive demand forecasting
However, implementation isn't without challenges. MIT Technology Review reports that 58% of failures stem from legacy system incompatibilities. Experts, like those at NAITIVE AI Consulting Agency, recommend a phased approach: start with sensor deployment, build cloud infrastructure, and train ML models before activating automated workflows.
For businesses that succeed, the benefits are clear. Most see a return on investment within 8-14 months through reduced inventory and waste. Companies using real-time analytics report 15-25% faster responses to disruptions and 30-40% fewer stockouts.
2. Fraud Prevention Systems
Fraud prevention has taken a leap forward with real-time data analysis, offering stronger security while keeping customer interactions smooth. These advanced systems can evaluate over 100 transaction details in just milliseconds, allowing for instant risk assessments and responses.
Many financial institutions have seen impressive outcomes with automated monitoring:
Metric | Outcome |
---|---|
Fraud Detection Rate | Over 95% accuracy |
False Positive Rate | Less than 1% |
Manual Review Reduction | 40-60% fewer cases |
Response Time | Under 100ms per transaction |
Take HSBC, for example. By leveraging AI-driven transaction analysis, they cut payment fraud by 65%. Their system evaluates multiple factors at once, such as:
- Device fingerprints
- Geolocation trends
- Historical spending habits
- Transaction speed
These systems operate on high-speed data platforms like Apache Kafka, which handles transactions with sub-second latency. This setup enables sophisticated detection methods like:
Detection Method | Benefit |
---|---|
Behavioral Analysis | Flags unusual activity patterns |
Graph Analytics | Exposes large-scale fraud networks |
NLP Processing | Reviews suspicious communication |
Collaborative AI Models | Shares insights across institutions for better results |
Lemonade, a leading insurance provider, highlights the efficiency of automation by processing claims in mere seconds. Their system checks over 50 risk factors, achieving detection accuracy above 90% while keeping false positives under 0.5%.
To succeed, organizations need to coordinate real-time data streams from systems like payment gateways and CRMs, supported by fast processing engines and automated response mechanisms.
The payoff is clear: companies often see fraudulent transactions drop by 60-80% within six months of implementing these systems.
3. Smart Inventory Control
With IoT sensors combined with live sales data, businesses can monitor stock levels instantly and automate restocking. This approach takes the IoT infrastructure used in supply chain optimization and applies it to fine-tuned inventory management.
Retailers using smart inventory systems have seen impressive outcomes:
Metric | Improvement |
---|---|
Stockout Reduction | 35-60% |
Inventory Costs | 15-30% savings |
Order Accuracy | Over 99% |
Restocking Speed | 50-70% faster |
Take Walmart as an example. By integrating real-time stock updates across 10 websites, they cut overstocking by 18%. Their success lies in syncing POS transactions, supplier deliveries, and warehouse movements in real-time.
Key technologies powering these advancements include:
- IoT sensors and RFID tags for precise item tracking
- Machine learning algorithms for accurate demand forecasting
These systems shine during disruptions. For instance, pharmaceutical distributors used predictive analytics to reduce emergency shipments by 65% during recent crises. By maintaining optimal safety stock levels, they shifted from reactive to proactive management. Machine learning models analyzing market trends and historical data have achieved forecasting accuracy of 85-92%.
"Smart shelf implementations reduce out-of-stock incidents by 43% and generate $2.8M annual savings through optimized replenishment."
Many successful systems use exception-based workflows. Routine tasks are automated, while anomalies are flagged for human intervention. This approach ensures efficiency while staying agile, especially during sudden demand spikes or supply chain hiccups.
4. Customer Experience Automation
Real-time data processing has changed the way businesses interact with customers across various channels. Modern systems can analyze behavioral signals and send personalized responses in milliseconds. This quick turnaround not only improves engagement but also drives sales, seamlessly connecting inventory management with direct customer interactions.
The benefits of automating customer experiences in real time are reflected in recent data:
Metric | Result |
---|---|
Conversion Rate Increase | 15-20% |
Average Order Value | +30% |
Mobile App Engagement | 25% higher |
Response Latency | Less than 500ms |
For example, Amazon's anticipatory shipping system uses browsing data to position inventory closer to potential buyers, cutting delivery times by 37%. This predictive approach has reshaped customer expectations around fast service.
Three key factors make these interactions possible:
- Data Processing Speed: Systems need to operate with latency under 500ms for time-critical tasks.
- Profile Management: Unified customer profiles integrate data from over 10 touchpoints.
- Compliance: Real-time adherence to GDPR and other regulations.
Machine learning plays a crucial role here. These models analyze customer behavior to trigger automated actions - like sending tailored email offers for abandoned carts or providing chatbot recommendations based on browsing history. Similar to predictive maintenance in machinery, these systems anticipate customer needs before they’re explicitly expressed.
Continuous improvements ensure that automation keeps delivering better customer experiences.
5. Equipment Maintenance Systems
Real-time data isn't just for customer engagement - it’s revolutionizing how physical assets are managed. Instead of reacting to breakdowns, companies are now predicting and preventing them. For example, manufacturing facilities using IoT-based monitoring systems have seen 25-40% fewer unplanned downtimes and extended equipment lifespans by 20-35%.
By analyzing patterns like vibration, temperature, and pressure, these systems can issue failure warnings up to 30 days in advance, helping to avoid costly overheating or other damage. They also connect directly to supply chain systems, automatically replenishing parts when needed - similar to Smart Inventory Control.
Key components for success include:
- Edge computing for real-time alerts
- Cloud platforms to track long-term trends
- Machine learning models to predict maintenance needs
- CMMS tools to schedule technicians efficiently
Take wind turbine operators, for instance. By using vibration data, they can time maintenance around favorable weather, cutting down on remote site visits by 40%. However, challenges like sensor calibration drift (affecting 23% of deployments) and overwhelming alert volumes (reported in 37% of cases) are common. Automated prioritization helps tackle these issues.
Here’s how these systems improve operational metrics:
Metric | Improvement |
---|---|
Unplanned Downtime | 25-40% reduction |
Maintenance Costs | 15-30% reduction |
Failure Prediction Window | 30-90 days |
These maintenance systems don’t work in isolation - they integrate with larger automation setups. Predictive algorithms can identify potential failures, check inventory for replacement parts, and adjust production schedules to avoid disruptions. This creates a seamless workflow, mirroring the efficiency seen in supply chain optimization.
Implementation Requirements
These five use cases rely on three main elements:
Core Technical Infrastructure
A solid foundation begins with scalable platforms for processing data streams. For example, Walmart's real-time e-commerce system operates on 250-node Hadoop clusters to handle simultaneous data streams.
Component Type | Required Capabilities | Performance Metrics |
---|---|---|
Stream Processing | Apache Kafka/AWS Kinesis | Less than 200ms latency |
Database Systems | Apache Cassandra | Real-time querying |
Edge Computing | IoT Gateway Support | 5-10ms response time |
Integration Architecture
To implement automated data pipelines, companies need standardized protocols such as MQTT for IoT devices and API-first frameworks. These ensure seamless communication between systems.
Security Framework
Modern systems require a robust, multi-layered security approach, which includes:
- Advanced encryption for live data
- Role-based access controls
- Real-time anomaly detection
- Behavioral biometrics
These measures are crucial for enabling fast transaction speeds and preventing fraud effectively.
Team Structure
Cross-functional teams made up of data engineers, DevOps specialists, and business analysts can accelerate deployments by 35%. This structure is essential for achieving automation objectives like predictive maintenance and improving customer experiences.
ROI Considerations
Most projects deliver ROI within 6-12 months by streamlining workflows. For instance, Jumio's systems prevent 94% of fraud before transactions are completed.
"Real-time systems detect 94% of payment fraud before completion, providing immediate ROI through loss prevention", states Jumio's implementation study.
To maximize success, organizations should begin with pilot programs in high-impact areas before scaling efforts across the board.
Conclusion
Real-time data automation is transforming businesses across various industries, offering measurable benefits that make a big impact. For example, companies using predictive demand forecasting have cut supply chain costs by 15-30%, while predictive maintenance systems have delivered $2-5M in annual savings per facility.
It’s not just about cost savings. These systems also help reduce risks. Financial institutions leveraging AI for fraud detection have seen a 60% drop in false positives, all while maintaining lightning-fast response times. This combination of efficiency and precision highlights the power of real-time automation.
Implementation Area | Impact |
---|---|
Supply Chain Costs | 15-30% reduction |
Fraud Detection | 95% accuracy |
Inventory Accuracy | 98% via IoT |
The future looks even brighter with new technologies on the horizon. Tools like digital twins for supply chain simulations, GenAI copilots for process improvements, and edge computing solutions are set to push automation capabilities even further. These advancements build on the foundational infrastructure already in place.
For businesses ready to take the leap, NAITIVE AI Consulting Agency offers the expertise needed to simplify the technical challenges. Their phased implementation approach ensures predictive systems are deployed effectively, helping organizations achieve automation goals without disrupting day-to-day operations.
FAQs
What are the advantages of real-time?
Real-time data processing allows businesses to quickly detect fraud, predict maintenance needs, and adjust inventory on the fly. These capabilities improve efficiency and speed up decision-making across various operations.
Today’s tools combine IoT and machine learning with existing ERP systems, making integration easier than before. For example, financial institutions can flag fraudulent transactions in milliseconds, while manufacturers cut costs by using predictive maintenance strategies.
Beyond operational improvements, real-time processing also enhances customer experiences, streamlines resource use, and strengthens risk management. This approach aligns with NAITIVE AI's phased automation solutions, which focus on delivering fast returns on investment.
To succeed, businesses need to ensure their IoT setups, machine learning models, and enterprise systems work together seamlessly.